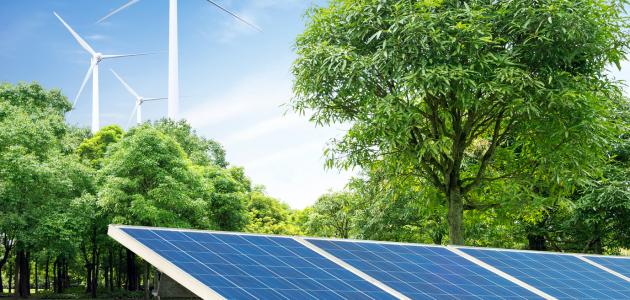
The fossil fuels means the main power generation; since the discovery of electricity until the present time; most of the energy production in the world relies major on it, but it is not permanent sources of power generation, it is possible that this source is drained in the end, this is in addition to other problems induced electric power generation from this source of environmental problems, and the fluctuation in the prices of energy and Glaiha; this is due to the high cost of extracting oil , and transportation, power generation use, and change its price always, due to the increase in the Aa recently; people are becoming aware of the need to go to the energy sources of clean and permanent electrical power generation, such as wind power, solar energy, and other different types of energy. [1] The Earth receives approximately 173 x 10 ^ 12 kilowatts of solar energy per hour, but part of this energy is reflected by clouds , oceans, and land, and another part is used to evaporate the waters of water bodies, and the solar energy is used in several ways, where it is used in heating systems. And the provision of heat, in addition to converting the solar energy into thermal energy using the solar cells . [2] The solar energy is one of the oldest sources of energy on the surface of the earth; the first furnace using the solar energy was manufactured in 1772 AD by the scientist Antoine Lavoisier. [3] Solar cells Solar Cells are photovoltaic panels that convert the solar energy into electrical energy through the photoelectric effect, so that the cell is made of semiconducting materials, which give it electrical properties when exposed to light, such as: electric current, voltage, resistance, and resistance The solar cell must also be able to absorb light and produce electrons. [1] The lifespan of solar cells of all types ranges between 10-30 years. [4] How to make solar cells at home Solar cells can be made at home using copper copper monoxide (Cu 2 O) as a semiconducting material, so it is the negative electrode in the cell, and copper is the positive electrode. [5] Tools used : copperplate. Sanding paper. Micro meter to measure the electric current. Large plastic packaging, or a glass container. Wires, or connectors. salt. Water. Electric heater . Metal scissors. Steps to make solar cells at home: To manufacture a solar home cell , follow these steps: [5] Cut the copper plate using the metal scissors to a size appropriate to the size of the heat source on top. Clean the copper plate after cutting it with a special soap or disinfectant; to remove any greasy material sticking to it, then clean it with sandpaper to remove the corrosion obtained, in addition to the copper sulfide lying on its surface. Putting the plate on a high temperature on the electric heater, you will notice the copper tinting in multiple colors as a result of oxidation, such as: red, orange, and purple, and when the plate is completely heated, it turns black, due to the formation of copper oxide. Leave the plate on the heater for half an hour, with the aim of condensing the black layer on its surface, then leave the piece on the gas after turning it off until it cools slowly, then the copper plate and the black layer formed over it shrink. Remove the formed black layer by rubbing it lightly by hand under the water, and it is worth noting that it should be avoided scraping this layer with sharp tools to avoid damaging the copper mono oxide layer formed. Bring another copper plate, and cut it the same size as the first plate. The copper plates are folded in a way that fits the plastic packaging, so that the face of the mono copper oxide formed on the first plate is out of the package, noting that the two plates are in contact with each other. Connect the positive electrode of the micrometer to the copper plate, and connect the negative electrode to the copper monoxide plate using the connection electrodes. Mix the hot water with two tablespoons of salt, then pour the mixture into the package, while avoiding immersing the two plates completely; to prevent contact with the water joints, leaving approximately one inch. When the solar radiation collides with the electrons on the surface of the mono copper oxide plate, the electrons gain enough energy that makes them free to move, which leads them to move in salt water, and they travel through the copper plate to electrical wires, so the microemeter needle moves, and it may give a reading ranging between 30-50 When the cell is exposed to sunlight , and a reading range of 0.5-0.6 أمA when placing the cell in the shade. [5] Types of solar cells and how to manufacture them The first generation of solar cells Manufactures solar cells in general semiconductor materials, such as crystalline silicon; where this production form of type approximately 90% of the cell industry solar in 2013, [4] The reason for the use of silicon heavily in the manufacture of solar cells because of the materials available in Great in nature, because of its reasonable price. It includes the first generation of solar cells, silicon solar cells, in both types: [1] Monocrystalline Solar Cells: This cell consists of one silicon crystal, and the efficiency of this type of cell reaches 17-18%; [6] that is, it can convert 17-18% of the rays falling onto it into electrical energy . Polycrystalline Solar Cells: They are formed from different crystals, and are made by melting the silicon , placing it in graphite molds, and then cooling it. The production rate of these cells reached about 48% of global production in 2008. This type is between 12-14%. [6] The process of manufacturing silicon cells generally begins with the manufacture of polysilicon (English: Polysilicon Manufacturing), as polysilicon is the main material for the semiconductor industry, which is a very pure silicone, and its cost is equal to a quarter of the cost of manufacturing the entire solar cells, after which this silicon is heated To the melting point, then the boron element is added to it to form a P-type semiconductor that carries the positive charge, then it is formed into blocks using casting or methods, then these blocks are cut into thin slices using wire saws with dimensions They are known as: (5 x 5) inches, or (6 x 6) inches in a circular shape, or a longitudinal or transverse rectangle, [4] and then the panels are cleaned, And placed in phosphorous ovens, to spread the phosphorus on the sides of the chips to form a layer of negative semiconductors (N-type semiconductors). [7] The reflectivity of the sunlight falling on the cell is reduced by spraying the chips with multiple layers of chemicals, or by making the surface more rough to reduce reflection, and increase the area over which the radiation falls, [4] after which the phase of printing the electrical conductors begins on the negative part of the chip, Its back is made of aluminum , and then tested the chips and assembled them in other factories in the form of solar panels, and put special layers of glass to protect the chips, increase their absorption capacity, and reduce reflection. [7] The second generation of solar cells The cells of the second generation of solar cells include morphine cells or thin-film cells (English: Thin-Film Solar Cells). Others, and these cells are divided into: [1] [6] Silicon morphine cells (English: Amorphous Silicon Thin Film (a-Si) Solar Cell): These cells are characterized by being amorphous, which is the type found in calculators , and this type of cell is made at temperatures as low as 75 degrees Celsius, where it is deposited Silicon is in the form of thin layers; its thickness reaches one micrometer on plastic surfaces , and the efficiency of this type of cell may decrease with time, as the value of the cell’s efficiency ranges between 4-8%, but it is able to work at elevated temperatures, And during changing weather conditions, that is, she is able to work in the area On days when there is less sun. Cadmium telluride cells (English: Cadmium Telluride (CdTe) Thin Film Solar Cell: This type contains a thin layer of cadmium telluride to convert solar radiation into electrical energy, and the manufacturing process begins by making cadmium telluride cells from crystal materials so that the glass is The main pillar of the cell, then the glass is coated with cadmium telluride layers, and this type is characterized by its flexibility, and its efficiency ranges between 9-11%, but the environmental risks related to the element of cadmium , and the possibility of its precipitation inside the bodies of living organisms make it one of the six toxic elements that cause the substance T on the face of the earth, which limits its use in the manufacture of solar cells. Copper Indium Gallium Di-Selenide (CIGS) Solar Cells: The effectiveness of these cells ranges between 10-12%, and is made by depositing a thin layer of copper , indium, gallium, and selenium On a layer of glass or plastic, with electrodes placed in front of and behind the cell to collect the electric current ; and due to the high absorption coefficient of this type of cell, a thin layer of it is able to absorb the sun's rays effectively compared to other types. The third generation of solar cells This generation includes new species that are still under research and development, and have not reached the stage of commercial industrialization, and include the following types: [6] Solar cells nanoparticles ( in English: Nano Crystal Based Solar Cells): The working principle of these cells to manufacture crystals of semiconductor materials; very small dimensions, measured Balnanomitr, ranging between 7-8% efficiency. Polymer Based Solar Cells: These cells are made using a polymeric material that is able to absorb solar radiation, and the efficiency ranges between 3-10%, and does not work well at high temperatures, but its cost is 50% less than the cells Silicon Solar. Solar cells Chromosomal (English: Dye Sensitized Solar Cells): manufacture these cellsfour parts, namely:thin layer of titanium dioxide component ofsemiconductor cathode,thin layer of oxide nickel binary component ofsemiconductor positive and material pigment sensitive to light, placed betweenpoles The cell, and a chip made of platinum or carbon, and its efficiency is approximately 10%, but it needs a lot of time to install compared to other types. Concentrated Solar Cells: The principle of these cells is to use many mirrors and lenses to produce high thermal energy , which is transmitted to thermal motors, and its efficiency reaches 40%, and is characterized by being thermally stable.
تعليقات
إرسال تعليق